Over the past years, we have taken many concrete measures that have resulted in substantially less dust emissions. We have built a new bay, realised an electrofilter installation and covered slag pits. We will continue working on limiting dust nuisance by commissioning a new dust removal plant, building a windbreak and installing additional roofs.
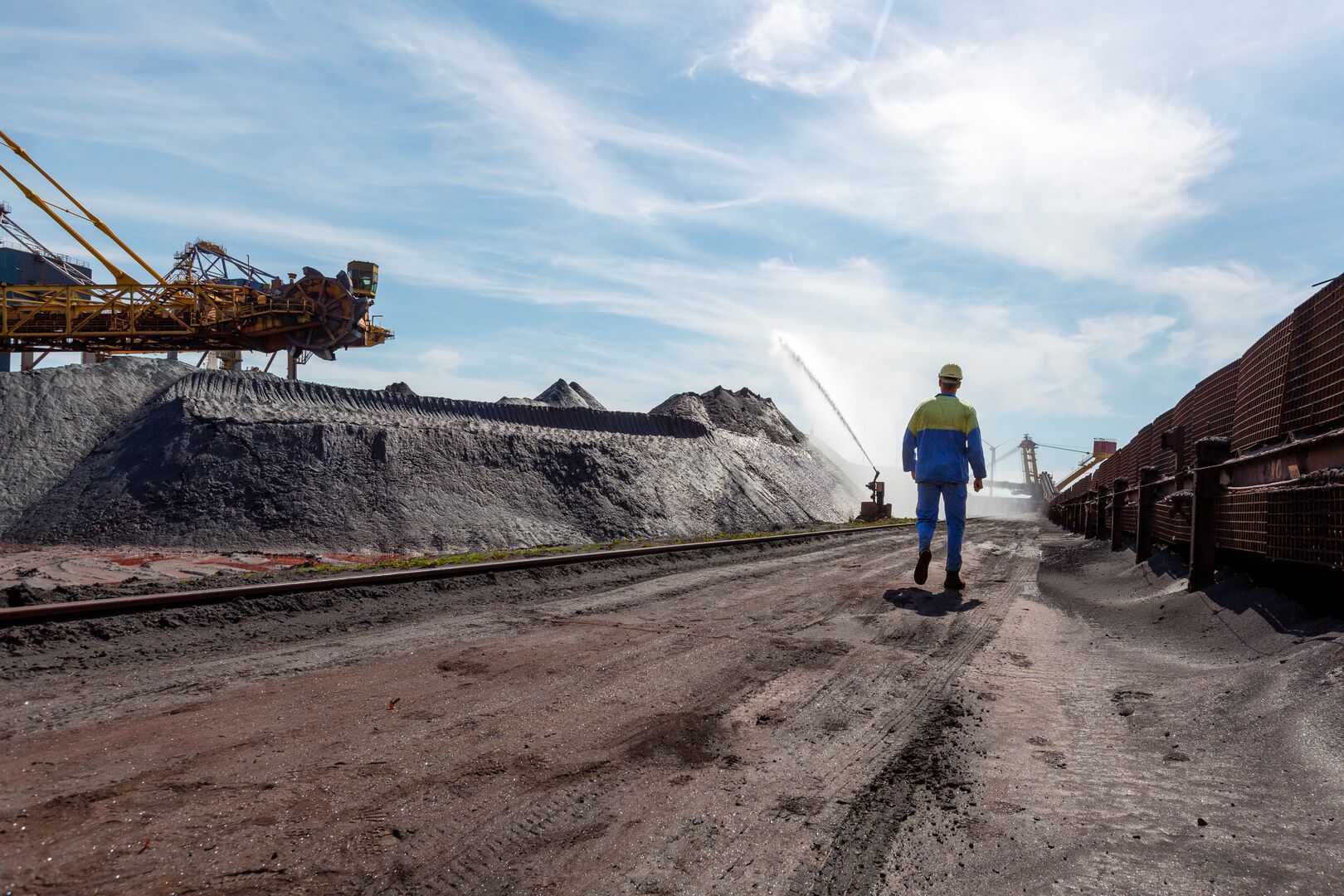
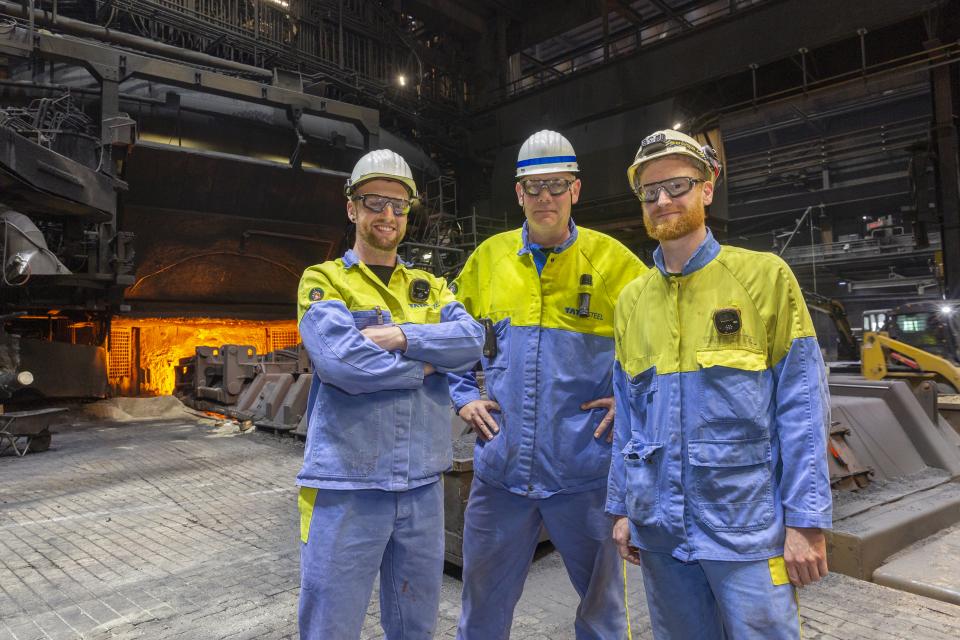
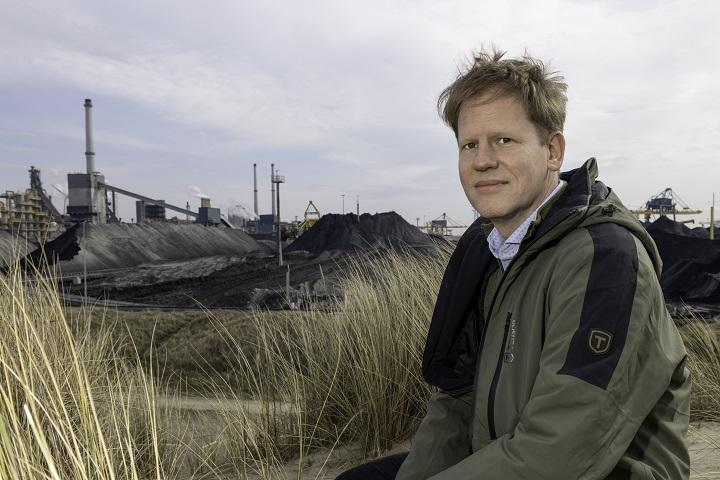
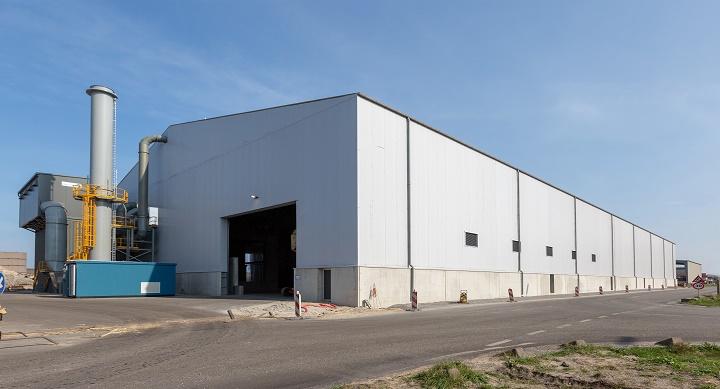
We are keen to realise major improvements in dust and heavy metals as quickly as possible. For example, a windbreak will be installed around the raw material storage facilities and we will be building the largest environmental installation ever at the Pelletising Plant. Various measures as a precursor to these major measures already seem to further reduce emissions of particulate matter, heavy metals and lead. The first results are promising. We will continue to monitor this to ensure these positive results are sustained.
Since the start of the Roadmap in 2019, we have taken various measures to further reduce dust emissions. As a result, less dust is deposited from our company premises in the immediate living environment. With Roadmap Plus, we are adding a whole package of new measures. We expect this to reduce the dust deposition of Tata Steel in Wijk aan Zee by approximately 65 per cent.
We expect a lot from the approach in the fight against dust blowing up at the storage fields and conveyor belts. We are further reducing visible dust with new measures. For example, by building a windbreaker of more than 18 metres high and more than a kilometre long. The windbreaker will be around the raw material storage facilities, thereby reducing wind speeds above this area. As a result, the wind has less grip on the material and less dust will be dispersed. There will also be covers for the blast furnace bunkers and the associated raw materials transport.
The important parts of the windbreaker will still appear this year. This is an important measure to further reduce dust blowing into the environment. Several specialists, including ecologists, have investigated the possibility of building a screen without adversely affecting flora and fauna. Such as on bats, for instance.
This has led to adjustments in the design. In the coming period, we will coordinate an adapted plan of action with the competent authorities and restart the permit process. We are making every effort to realise the windbreaker as soon as possible. We plan to complete the entire screen in the first half of 2024.
In April 2022, we commissioned a number of new slag pits with a mobile covering. From now on, the entire converter slag flow is cooled under a cover. A thick mist curtain ensures that as much dust as possible remains in the pit and that any dust that is released precipitates immediately. We expect this process to generate a reduction in dust emissions of approx. 80%.
Dust samples show that, with the Roadmap Plus, we have already taken a big step in the field of slag dust. Sample analyses show that the amount of slag dust in the environment has decreased, from on average 50% in the first half of 2019 to on average 15% in the first half of 2022. This is with the exception of peaks due to incidents.
Since the end of 2021, we have had dust samples taken at various locations in the area under the supervision of TNO. We analyse these dust samples to determine their origin.
We also analyse the concentration of metals in the dust in accordance with the investigation method of the Dutch Institute for Public Health and the Environment (RIVM). This helps us make our results comparable with those of external studies, including those of the RIVM.
In the past decade, we have already undertaken a lot to reduce the emissions of heavy metals, such as lead and particulate matter. Lead emissions from the site have already been reduced by 95%, mainly as a result of the bag filter installations at the Sintering Plant. We are pressing ahead with the construction of a dust removal installation and a DeNOx installation at the Pelletising Plant. This will be our largest environmental installation ever. Together with a number of other measures, this will help us reduce total lead emissions even further in 2023, by approx. 70% (70% of 5%). In addition, heavy metal emissions will be reduced by approximately 55 per cent, and particulate matter emissions by some 35 per cent. These reductions are in comparison to levels at the start of Roadmap 2030 in 2019.
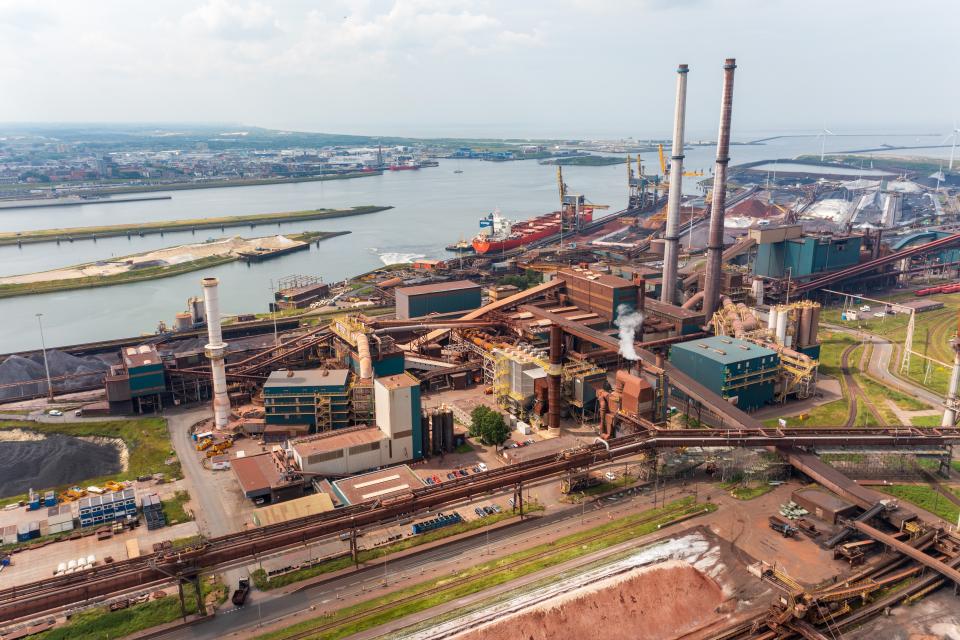
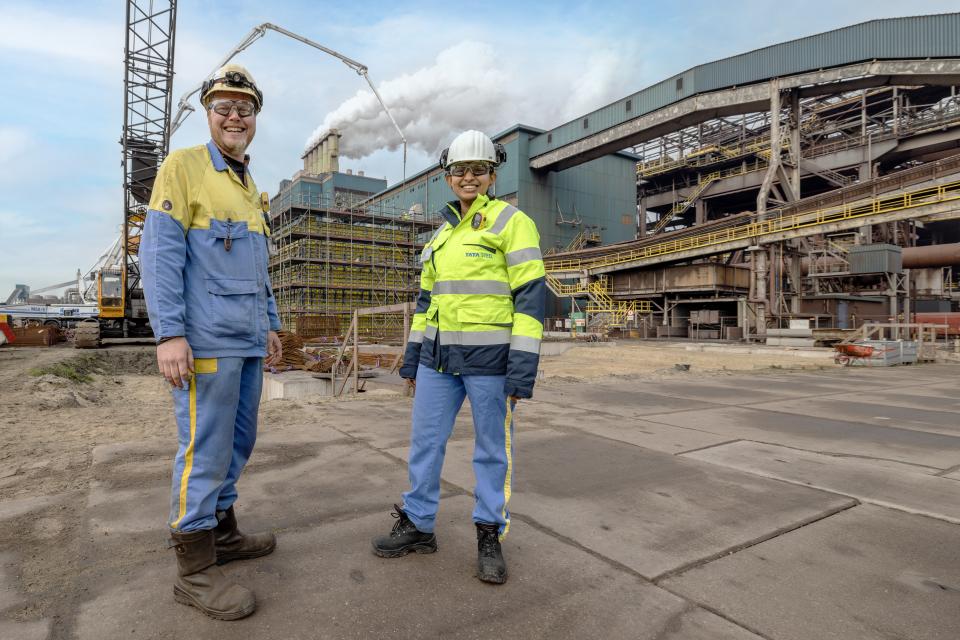
The Pelletising Plant will have a dust removal plant fitted. In addition, there will be a DeNOx installation to further reduce nitrogen oxide emissions. A team of technical experts has been working on a smart design over the past year, which means that we can start on the new dust removal plant earlier than expected. Thanks to this expansion, we expect to reduce emissions of dust, lead and other heavy metals by approximately 80% at the Pelletising Plant by 2023, compared to 2019.
Although the realisation of the dust removal plant is not easy, we don’t want to wait for the entire project to complete to reduce emissions. In order to achieve results faster, we looked at what is possible in the very short term. We have already taken various measures. For example, the fluorine scrubbers, which currently fulfil the function of the future dust removal plant, have been fitted with new nozzles that capture dust and heavy metals even better. As a result, we see a reduction in particulate matter, heavy metals and lead in our preliminary results. We will continue to monitor this to ensure these improvements continue.
In the coming period, we will be installing additional exhaust systems on the roofs of our BOS Plant and Blast Furnaces. We have now installed one extra exhaust hood at the Blast Furnaces. Five more will follow next year, spread over the two Blast Furnaces. These are expected to reduce dust emissions during the tapping of hot metal by approximately 75%. The BOS Plant too is ready to take an additional exhaust system into service next year. This exhaust system will be even more effective in the targeted extraction of flue gases in the steelmaking process.
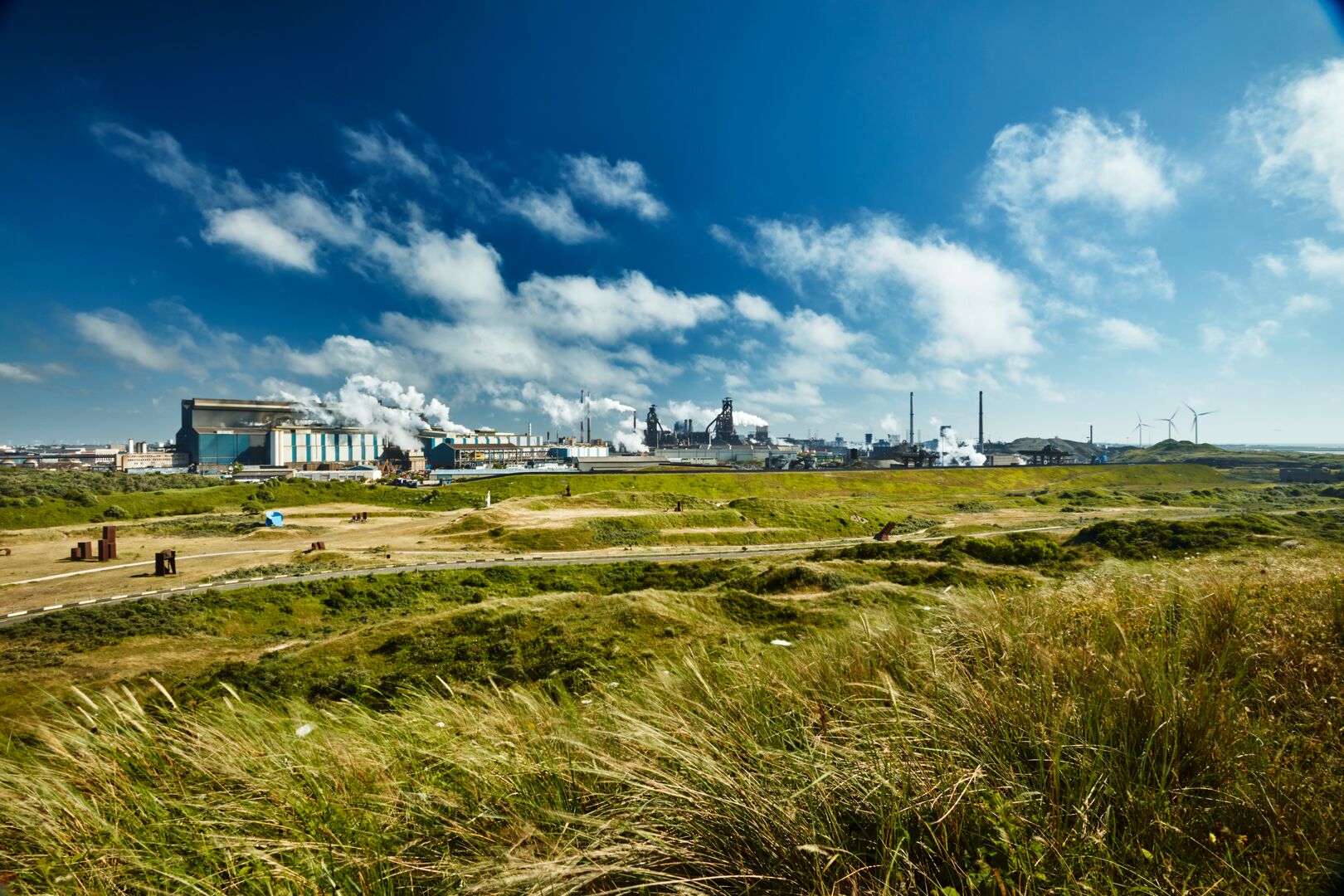
More information about Roadmap Plus
Our overviews contain more information about the Roadmap Plus and the measures we are taking.