Dust that is released during our work may end up in the environment. We have taken various measures to reduce this. Now we are pressing on with the Roadmap Plus: additional measures and accelerated measures to reduce dust and heavy metals emissions as much as possible.
We continue working on a new dust removal plant - part of the largest environmental installation ever - at the Pelletising Plant and expect to install additional exhaust systems at both the Blast Furnaces and the BOS Plant. We also want to further reduce dust deposition by constructing a large windbreak around the storage facilities and covering the Blast Furnaces bunkers.
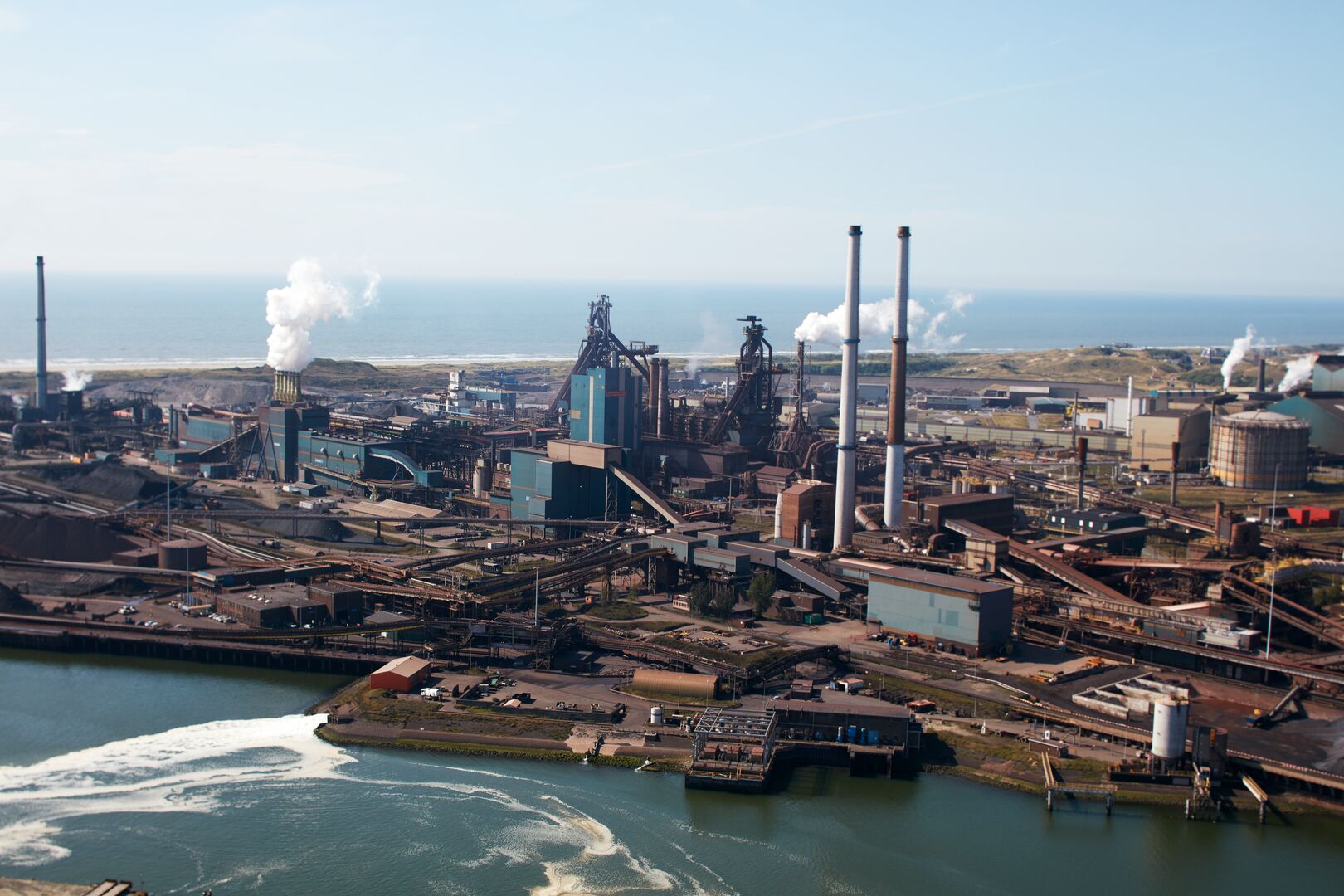
Our dust deposition reduction measures
Converter slag is a by-product of the steelmaking process. Before Harsco - the slag utilisation company on our site - processes the slag, it is cooled with water in what are known as slag pits. During this process, dust can spread as a result of the steam that rises in the warm air.
Since April 2022, we have been working with a number of new slag pits, with a mobile covering. Now we no longer have to cool converter slag in the open air, but can do so under a cover. This results in less dust emissions. A thick mist curtain ensures that as much dust as possible remains in the pit and that any dust that is released precipitates immediately. We expect this process to generate a reduction in dust emissions of approx. 80%.
On our site, we store various raw materials that we need to produce high-grade steel, including coal and ore. We continuously try to prevent dust drift from these storage facilities as much as possible. But when the storage facilities are excavated or when the raw materials are moved to the plants on the conveyor belts, the wind may nevertheless blow dust into the environment.
By realising a huge windbreak along the entire site of the coal storage facilities, we can significantly reduce dust drift. The structure will be over 18 metres high and just over a kilometre long. The purpose of the windbreak is to reduce the wind speed above this area. As a result, the wind has much less grip on the material and less dust is dispersed. In addition, it can capture any dust particles that do end up in the air before they drift into the environment.
We transport raw materials such as sinter, pellets and coke on conveyors to the Blast Furnace bunkers. As these substances are warm and dry, this route is susceptible to dust dispersal. To prevent this as much as possible, we keep the raw materials wet during transport. But dust can still be blown up when material is tipped in the bunkers or from one conveyor to another. That is why we will largely cover the bunkers and conveyors and filter the dust by extracting it.
At Raw Materials Logistics, we transport and process the raw materials that we receive, such as ores from and to the Sintering and Pelletising Plant and coke to the Blast Furnaces. Because we work with different sand-like raw materials, we do a number of things to further reduce dust dispersal in raw materials logistics, for example installing tyre washers, renewing overflows where raw materials fall from one conveyor belt onto another, renewing and improving water pipes and spray nozzles and installing extra environmental cameras.
Our measures to reduce dust emissions and heavy metals
In the Blast Furnaces we produce hot metal – the core ingredient for steel production. The hot metal goes from the so-called 'tapholes' of a Blast Furnace to the BOS Plant by means of special trains.
Dust may be released when these tapholes are opened and closed. That is why both Blast Furnaces have been fitted with a dust removal plant to extract dust. We will be installing six additional exhaust hoods to reduce dust emissions during the tapping of hot metal by approximately 75%.
Another important measure we are taking is the installation of an air screen above the chute in both Blast Furnaces. Any dust that is released is collected at the extraction points by means of a push-and-pull system. The first tests at Blast Furnace 6 have been completed and appear to be a success. This year, we will continue with Blast Furnace 7.
In the Blast Furnaces we produce hot metal – the core ingredient for steel production. The hot metal goes from the so-called 'tapholes' of a Blast Furnace to the Steel Plant by means of special trains. Dust may be released when these tapholes are opened and closed. In the coming period, we will be placing additional exhaust systems to reduce dust emissions during the tapping of hot metal by some 75%. In total there will be six new extractor hoods, divided over both Blast Furnaces. The first additional hood has already been installed and we expect to have all hoods fitted this year.
In addition, we are also improving the tapping process. To this end, we are installing innovative software that continuously monitors the tapping process and gives a signal to close the tapholes on time.
The BOS Plant converts hot metal into steel. We will install an additional exhaust system for improved extraction of dust-containing flue gases during the tipping of hot metal into the converter (large ladle) and reduction of emissions through the roof. Two of the systems are already in place, but because dust is still being released through the roof, we will install a third one. We intend to complete this measure next year.
The Pelletising Plant processes iron ore into pellets for use in the Blast Furnaces. We can substantially reduce the emissions of this production process by means of a DeNOx installation and a dust removal plant. This new high-tech environmental installation, involving a total investment of EUR 200 million, is expected to reduce lead, heavy metals and dust emissions at the Pelletising Plant by approx. 80% in 2023 compared to 2019.
Clean more quickly
In order not to lose momentum, we have separated the construction of the dust removal plant from that of the DeNOx installation. This will allow us to commission the dust removal plant in 2023 and accelerate lead, heavy metals and dust emission reductions.
How does it work?
The flue gases that are released during the production of pellets are transported to the new dust removal plant through a special pipeline. This pipeline is 140 metres long and has a diameter of 6 metres. This is comparable to the cross section of a tunnel tube of the North-South line tunnel in Amsterdam. The dust removal plant itself consists of more than 6,000 filter bags, all together more than 60 km long, which subsequently clean the flue gases to reduce the emission of dust and heavy metals at the Pelletising Plant.
30% fewer nitrogen oxides
The second part, the DeNOx installation, will be commissioned in 2025. With this installation, we will reduce nitrogen oxide emissions at the Pelletising Plant by as much as 30%. For this, we use a new technology that has not yet been applied on this scale elsewhere in the steel industry.
In 2021, we built a second electrofilter installation at the Sintering Plant. This large environmental installation (15 metres wide, 30 metres long and 30 metres high) is over three times the size of the first electrofilter installation and significantly reduces emissions of dust from the Sintering Plant.
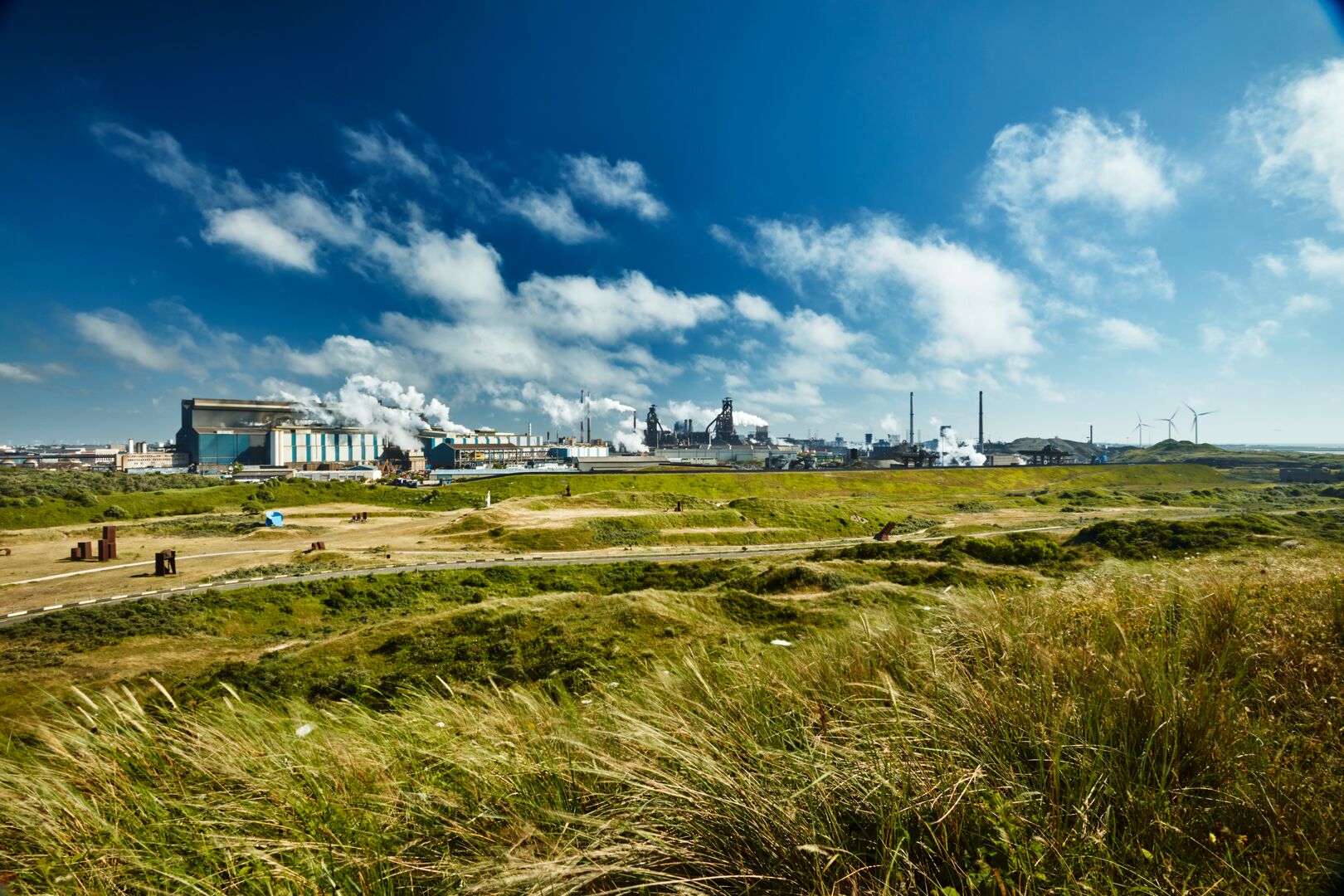
More information about Roadmap Plus
Our overviews contain more information about the Roadmap Plus and the measures we are taking.