Roadmap 2030 marks the start of various measures to reduce dust emissions. These have already significantly decreased the share of slag dust in samples in Wijk aan Zee. A key pillar for this was the commissioning in June 2020 of the new bay for ROZA slag utilisation.
The share of converter slag dust in the environment has also been decreased. This is partly due to the fact that we have removed the protective layer from the slag ladles so that no pulverised layer is released during tipping. We have also thoroughly analysed and adjusted the converter process in the BOS plant, so that converter slag can be utilised more effectively and dust emissions have been reduced. Other examples are measures taken in ore preparation (spraying poles and misting installations) and the removal of two emission points at the Sintering Plant.
In the Roadmap progress report we look back at the past year and a half.
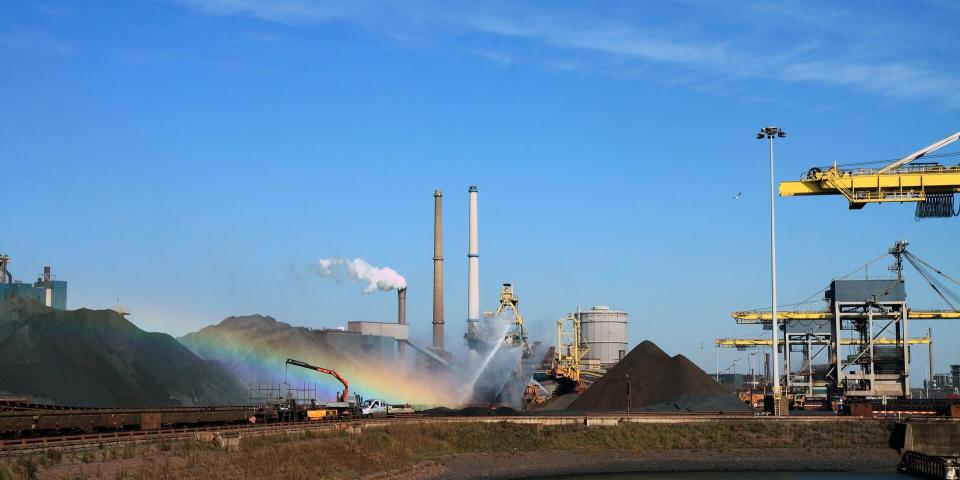
Our measures against dust deposition
We have made major strides in terminating graphite nuisance for the community.
Because this type of slag (ROZA slag) is now utilised in the new bay, the risk of graphite dust spreading to the environment during this process is a thing of the past.
In the bay, flat trays are used instead of ladles. As a result, the two pig iron desulphurisation plants (ROZA) of the BOS Plant that pour the slag into the ladles had to be converted. This way, the flow of ROZA slag can be collected in flat trays and subsequently utilised in the new bay. Moreover, the main areas around Harsco have been asphalted. This makes it easier to keep the site clean and optimally prevents dust being blown up by logistical movements.
To prevent nuisance, Tata Steel has adjusted the production process and taken additional measures in the slag utilisation process at Harsco. The process has been adapted in such a way that the cooling times of the ladles with ROZA slag are structurally above 16 hours. We achieved this by limiting the amount of slag per ladle, significantly expanding the number of slag ladles, purchasing extra wagons and renovating the cooling track.
Construction of the bay for ROZA slag utilisation has since been completed. Because this type of slag (ROZA slag) is now utilised in the new bay, the risk of graphite dust spreading to the environment during this process is a thing of the past.
Dust analyses showed that utilisation of converter slag causes a lot of dust-related complaints in the community. We see that the share of converter slag dust in the samples from Wijk aan Zee has decreased considerably since the end of 2020. In November 2019 and January 2020, the dust in Wijk aan Zee still contained 40% to over 60% of slag particles, while from February this fell below 20%, with the exception of one peak in September 2020.
The structural reduction in the share of converter slag is partly due to the fact that we have removed the protective layer from the slag ladles so that no pulverised layer is released during tipping. We also tip this slag into the pit from a minimal height. Moreover, we have thoroughly analysed and adjusted the converter process in the BOS plant, so that converter slag can be utilised more effectively and dust emissions have been reduced.
In April 2020, we conducted a trial that showed that the cooling process after tipping could be improved. Adjustments that have since been made also reduce the amount of dust released during cooling and excavating converter slag. During the trial, we also installed a prototype covering over an open converter slag pit.
Important unpaved roads and parts of the site have been asphalted to prevent the spread of dust caused by transport movements on the slag utilisation site as much as possible.
This makes it possible to drive energy-efficient vehicles. What’s more, cleaning the site will be easier.
Removing Sintering Plant emission points
In September 2019, we removed two emission points, reducing particulate matter emissions from the Sintering Plant.