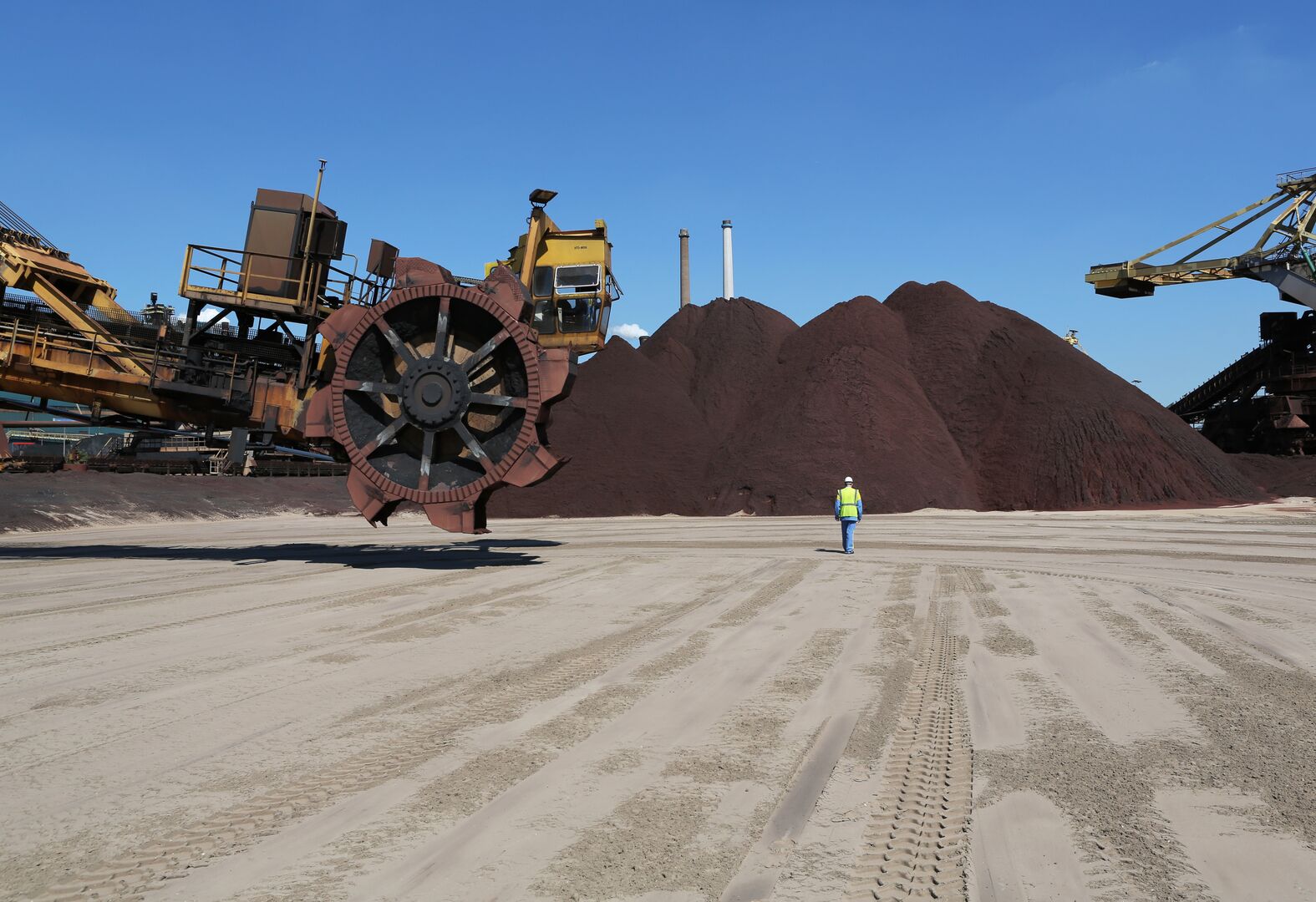
Here, coal is heated for 18 hours to 1,000 degrees Celsius. The coal mixture turns into hard chunks of coke, creating coke gas that powers other plants on our site. When the cokes are 'done', they are immediately quenched with water. This creates impressive plumes of steam. After this, the coke is ready for use in the Blast Furnaces.
Coke quenching is a standard process that is repeated every 15 minutes. It releases the distinctive white plumes that you see above our company, often two simultaneously since we have two coking plants. Our own research shows that standard quenching yields the best result in terms of dust emissions.
The figures:
- Coke production: 1.8 million tons a year
- Coke oven gas produced: 115,000 m3 per hour
- Of these gases, 100% is reused
From the mixing heap, ores travel on a conveyor belt to two plants to be fired into sinters and pellets. The Sintering Plant produces lumps of ore (sinter) and the Pelletising Plant makes smaller, hard pellets.
A modern bag filter installation filters the flue gases. This helps minimise dust and particulate matter emissions.
The figures:
- Pellet production: 4.8 million tons a year
- Sinter production: 4.8 million tons a year
- 25% of the residual products from the Sintering Plant is reused
- 2025: completion of DeNOx installation at Pelletising Plant
The two large Blast Furnaces are continually fed from the top with coke, pellets and sinter. Hot air and pulverised coal are blown into the bottom of the furnaces, creating a temperature of well over 2,000 degrees Celsius. The resulting chemical reactions produce liquid iron and liquid slag. These are tapped and separated.
The iron flows into a special refractory train wagon, also called a 'torpedo', which takes it to the BOS Plant. The liquid slag is cooled with water, creating a high-grade quality of slag sand, which is used as a raw material for mortar.
The figures:
- Height: 120 metres
- Pig iron production: 6.5 million tons a year
- Highest temperature: 2,300 degrees Celsius
Liquid iron and steel scrap are fed into a converter: a large vessel of approximately 11 by 9 metres. By blowing oxygen into this vessel, carbon is removed from the iron and steel is created. We then produce the steel exactly to the customer's specifications. In the casting machine, the steel is poured into slabs weighing 15 to 40 tonnes. We reuse large quantities of steel scrap in the BOS Plant. The new steel we make will come back as scrap at some point: an eternal cycle.
The figures:
- Height: 86 metres
- Steel production: 7 million tons a year = 280,000 slabs of steel
- 25% comes from recycled scrap
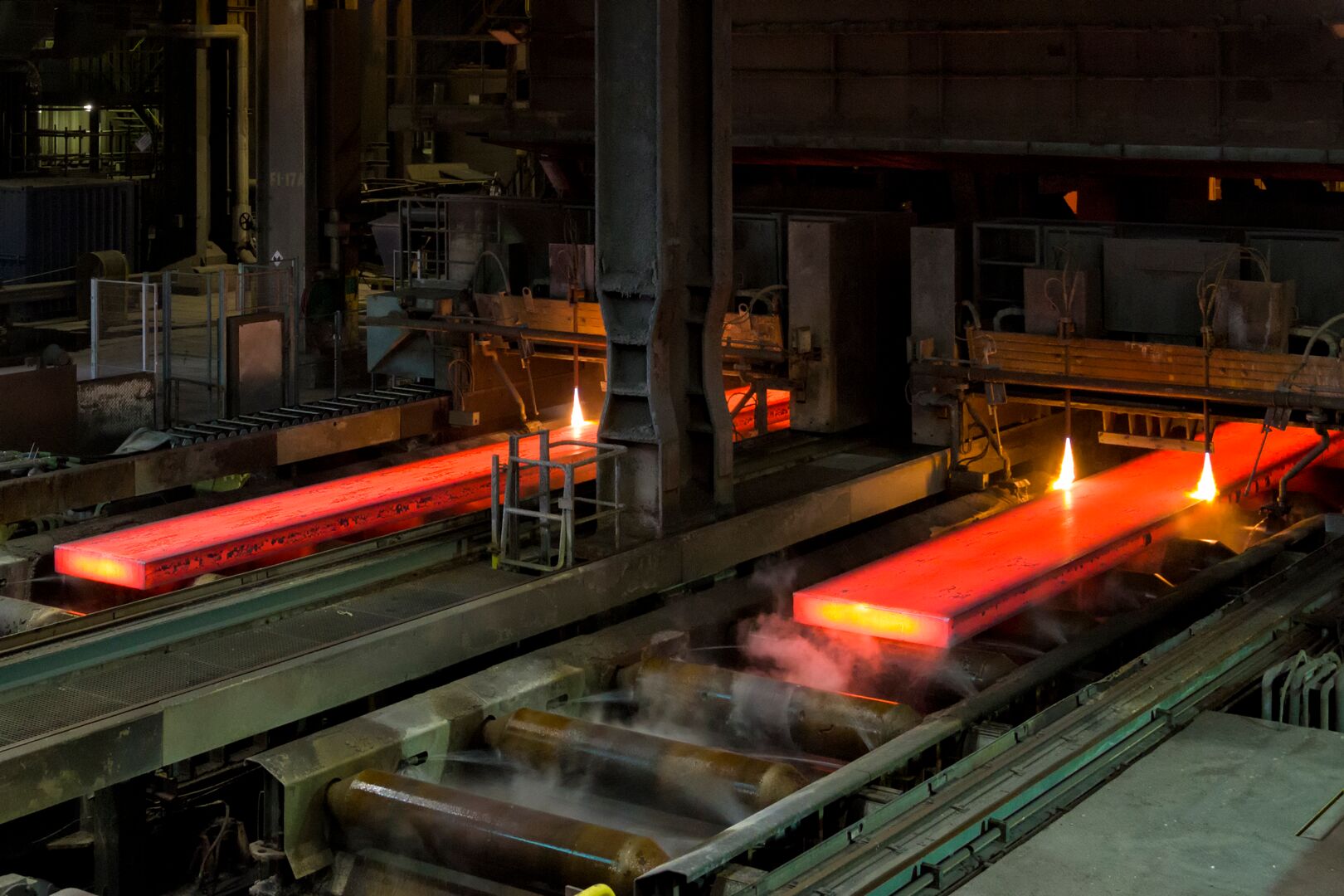
In the Direct Sheet Plant the liquid steel is formed into rolls of hot rolled steel in one continuous and efficient process. This steel is used in electrical components, such as fins for electric motors and parts for transformers. It is also used in car seats, furniture, and façade sections.
The figures:
- 1.4 million tonnes of steel produced per year (70,000 rolls)
- Length of tunnel furnace 320 metres
In the Hot Rolling Mill, slabs of steel are heated in a furnace before being rolled out. We can make steel as thin as 2 millimetres. It is then cooled down and rolled up. Through the process of heating, rolling and cooling, we can determine precisely what kind of steel we want to make. Whether example malleable steel for battery cases, or extremely strong steel for diggers.
The figures:
- Production capacity: 5.3 million tonnes a year = 267,000 rolls
- Maximum weight per roll: 38 tonnes
- Length per roll: Maximum 2 kilometres (for the thinnest material)
On the Pickle Line, the mill scale is removed using diluted hydrochloric acid. The mill scale is an oxidised layer that occurs during hot mill rolling. The removed oxide is collected and used later as raw material. After pickling the rolls are coated with a layer of oil to prevent rust.
The figures:
- Production capacity: 4 million tonnes a year
Through cold rolling the steel becomes thinner, smoother and stronger. After rolling, large protuberances form below the steel, which makes it easier for us to process it. Cold-rolled steel is used for various purposes, for example in domestic appliances. A proportion of these rolls goes through to the next production phase to protect the material against rust and thereby make it more durable.
The figures:
- 2,4 million tonnes a year
- Weight of roll: 10-48 tonnes
- Thickness of strip steel: 0.3-4 mm
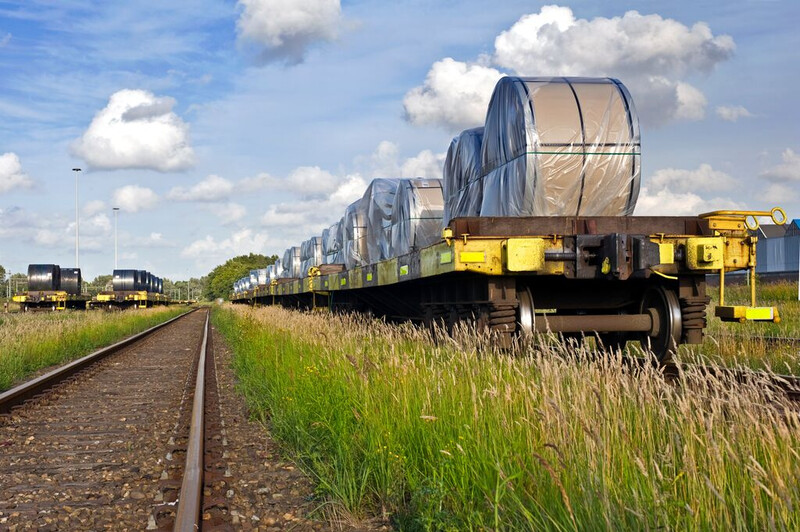
On the Galvanising Line, a layer of zinc is applied to the cold- or hot-rolled pickled rolls to prevent corrosion. This galvanised steel is used in cars or façade panels, for instance.
The steel undergoes a number of stages before a layer of zinc containing magnesium and/or aluminium is applied in a bath. We increase its durability with Magizinc®. This is one of our special coatings with which we offer double protection against rust with less zinc. Besides galvanisation, refining also takes place.
We carefully monitor the quality of the steel surface. Advanced and automated inspection systems ensure good monitoring.
The figures:
- Height of looping tower 30 metres
- Rolls of steel: 1.6 million tonnes galvanised, of which 1/8 were painted rolls
- Maximum speed of 180 metres per minute
In packing-steel production lines, the steel is pickled, cold-rolled and heated so that the material becomes softer and more malleable. This makes it suitable for example to make beverage or aerosol cans. The thin sheet steel also gets another thin layer to prevent corrosion. In addition, we coat packaging steel with a thin layer of Protact® polymer to make it safe for foodstuffs. About 95% of all packaging steel in the Netherlands is recycled into new steel. Tin plate is therefore the most circular and sustainable packaging material.
The figures:
- 0,8 million tonnes produced per year, of which 95% is tinned
- Thickness of strip steel: 0.14 – 0.5 mm
- 95% of all used cans is recycled into new steel
On our site we transport rolls of steel from one production facility to another. In the end it is packed to be shipped from the departure points to our customers. The shipment of our steel is done:
- 1/3rd by sea
- 1/3rd by barge
- 1/6th by train
- 1/6th by lorry
The figures:
- 100 kilometres of track, 345 switches, and 90 crossings
- 350.000 rolls of steel a year
We have our own energy company. It supplies us with production gasses, steam and electricity from our own power plants.
Production gasses are by-products from the coking and gas plants, blast furnaces and steel plant. We (re)use two thirds of it ourselves. The rest goes to the Vattenfall power plant which in return supplies us with electricity.
The figures:
- We produce 15% of our own electricity needs
- The blast-furnace gas pipeline is 2.5 km long with a diameter of 3.2 metres